CASE STUDY:
Cardinal Indicator Egg Sorting Application
National Poultry Equipment Company (NPE), based in Iowa, produces egg processing equipment for small-to-medium sized egg producers across the globe. The types of eggs processed span from traditional sources, such as chickens, to more exotic varieties, namely game birds. NPE provides well-functioning, affordable, and reliable machinery to their clientele. Most importantly, NPE provides their customers with systems that fit their clients’ needs and capacities, which is where Cardinal Scale enters the picture. Introducing NPE’s digital egg grading system.
NPE utilizes Cardinal’s 210 indicators and custom application software as a solution to meet their variable customer base. Due to differing dimensions between poultry species, NPE needed an indicator with a plethora of options to guide the sorting process with their machinery. Cardinal’s 210 indicator offers an expanse of features perfectly suited to their customers’ operations.
The Cardinal 210 indicator’s functions are the final step of a multi-step process in NPE’s Sani-Touch CSG series machinery. Eggs are placed on a cross-loader leading to a spool spinner candler, positioning the eggs in a uniform manner laying horizontally. Eggs are “candled”, meaning a light is illuminated through the egg to check for egg shell quality such as cracks or yolk imperfections such as blood spots. The eggs are then transferred onto a conveyor chain and passed through a metal tank enclosure where a water-based sanitizing solution is applied and rapidly revolving, soft nylon brushes wash and sanitize each egg. A second set of brushes then dries the egg before exiting the sanitizer where the egg “grading”—separation based on size—can begin. At this point, the 210 indicator will begin its integration.
Programmed into the 210 indicator are six preset egg weights determined by the operator: small, medium, large, extra-large, jumbo, and anything falling outside of the aforementioned parameters as a reject. Eggs are optically scanned for placement and weighed, which are read and stored in the 210 indicator. The eggs are then moved along the conveyor chain where five differently located “rotary kickers”—an implement that pushes the egg off of the conveyor chain—receive a signal from the 210 indicator and push each egg into their respective grading station determined by their weight. While all of this is going on, the Cardinal 210 stores and recalls the number of eggs per grade.
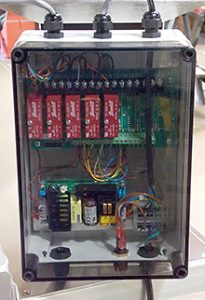
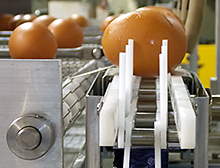
In addition, the Cardinal 210 also offers many other advantages that may also be utilized from its software. Counters may be used to track each grade’s total weight. Average weights can be tallied for each class within each flock. Counters and accumulators can be saved for up to ten different flocks. And each grade can be assigned to one or many kickers simultaneously.
The Cardinal 210’s great flexibility and easy programming are of great benefit to the many customers of NPE. “Our customers sell to a variety of markets such as restaurants, farmer’s markets, local and national grocers, and vaccine research companies. Being able to change weights quickly to meet their outlet’s specifications is a great benefit,” states Justin Enzinger, former President of National Poultry Equipment Company.

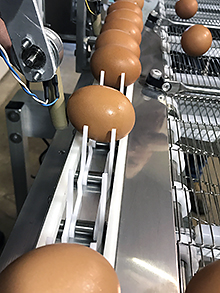
The synthesis of NPE’s Sani-Touch model design and Cardinal’s 210 indicator technology coheres multifaceted processes into an easy and effective unit. This fusion of implements can yield up to 10,800 eggs being candled, sanitized, and graded per hour. Such output capacity helps keep small-to-medium producers competitive for many years to come.
( Sourced and published by Cardinal/Detecto. https://cardinalscale.com/news/news-events-article/case-studies/case-study-cardinal-indicator-egg-sorting-application )